How Are Water Bottles Manufactured?
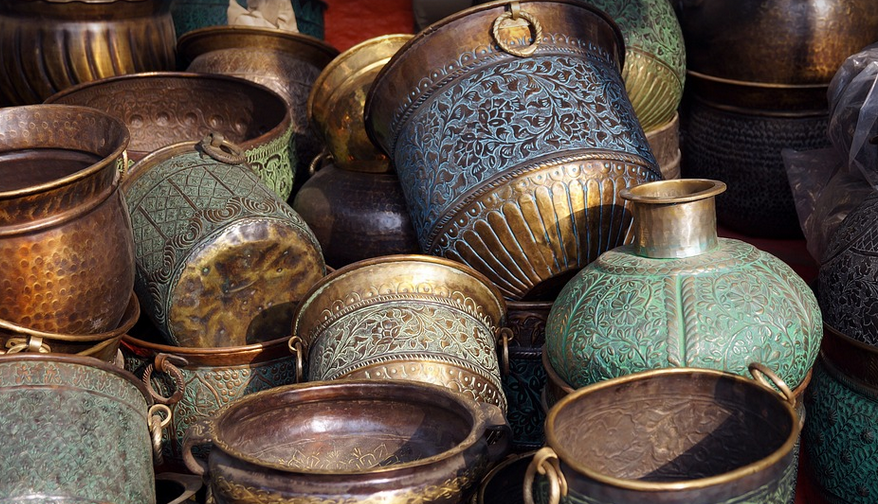
The Journey of a Bottle: From Raw Materials to Your Hands
Water bottles are ubiquitous in modern life, accompanying us on our daily journeys and helping us stay hydrated. But have you ever wondered about the intricate manufacturing process behind these seemingly simple containers? The journey from raw materials to your hands is fascinating, showcasing the ingenuity of engineering, design, and meticulous craftsmanship.
It all starts with a vision: the perfect design for a water bottle that caters to specific needs like durability, insulation, or eco-friendliness. This visionary spark often leads to the creation of 3D models, allowing designers to visualize and test their designs virtually before ever bringing out any physical prototypes.
Once the design is finalized, the journey into creating a water bottle begins! The first step involves procuring raw materials like plastic, metal, or even glass. These materials are carefully selected based on factors like chemical resistance, durability, and sustainability. For instance, PET (polyethylene terephthalate) is a popular choice for plastic bottles, known for its lightweight nature and ability to withstand high temperatures.
Next up: shaping the raw material! This often involves using advanced manufacturing tools like injection molding or blow molding. Injection molding uses heated liquid polymers that are injected under high pressure into molds forming intricate shapes. Blow molding, on the other hand, inflates pre-formed plastic pellets into a bottle shape, creating its characteristic streamlined form.
The production of metal bottles is slightly different. In this case, sheet metals like aluminum or stainless steel are cut and formed using industrial presses and welding machines to create precisely shaped containers. The final product is often polished for aesthetic appeal and enhanced durability. For glass bottles, a more ancient form of material crafting involves melting sand at extreme temperatures to form molten glass. This molten material is then carefully shaped and cooled into the desired bottle shape.
Now for the finishing touches! Once the bottles have been manufactured, they undergo rigorous quality control checks. These inspections are designed to identify any defects or imperfections in the bottles, ensuring consistency and reliability in their performance. This meticulous scrutiny involves visual inspection, pressure testing, and chemical analysis, all of which play crucial roles in maintaining the high standards associated with bottled water.
After passing quality control, the water bottles get packaged for distribution. These packages could be simple cartons or intricate designs incorporating branding materials like logos and slogans. The final packaging often acts as a first impression, building brand recognition and adding value to the product. Packaging also ensures proper protection during shipment and helps maintain the integrity of the bottles.
Finally, the bottles reach their destination – your hands! Whether it’s at a grocery store aisle, a convenience shop, or even directly from a water filtration company, getting your hands on a bottle is an accomplishment in itself. This journey from raw materials to a convenient and accessible container highlights just how much goes into ensuring you have access to clean, safe, and enjoyable hydration.
The next time you reach for your favorite reusable water bottle, take a moment to appreciate the intricate process that brought it to life. From vision to final product, every step tells a fascinating story about human ingenuity and the relentless drive to create practical solutions in our busy world.